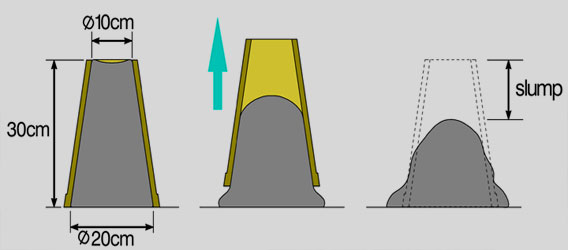
Concrete Slump Test
The slump cone is used for determining the workability of concrete where the nominal maximum size of aggregate does not exceed 38 mm.
B. Methods of sampling and analysis of concrete
1. Firstly decide the frequency of slump value to be taken during concreting.
2. Oil the interior surface of the slump cone with mould releasing oil to prevent adhesion of the concrete.
3. Place the slump cone on a leveled surface.
4. Collect the sample in a wheelbarrow after mixing the concrete properly in the transit mixture.
5. Remix the sample thoroughly in wheelbarrow with sampling scoop.
6. After remixing immediately fill the slump cone in layers approximately one – quarter of the height of the cone.
7. Each layer shall be compacted with the tamping rod by 25 strokes distributed in a uniform manner over the cross-section of the cone and for the second and subsequent layers tamping rod shall penetrate into the underlying layer.
8. After compacting the top layer the concrete shall be struck off level with the top of the slump cone, using a _______. Any mould which may have leaked out between the mould and the base plate shall be cleaned away.
9. Unscrew the slump cone from the base plate and remove it immediately from the concrete by raising it slowly and carefully in a vertical direction.
10. After the concrete subsides place the slump cone on the base plate in reverse position and place a scale on it. Measure the height between the top of the mould and the highest point of the concrete specimen being tested.
C. Reporting of slump value: The slump measured shall be reported in terms of millimeters.