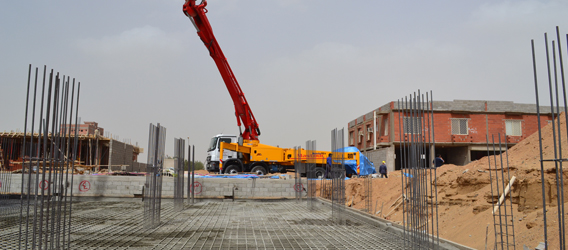
Concrete Construction
The term ‘Foamed Concrete’ may be somewhat misleading in that most do not contain large aggregates (indeed it may be considered to be foamed mortar or foamed grout). It is a lightweight concrete manufactured from cement, sand or fly ash, water and a preformed foam. Its dry density ranges from 300to 1600kg/m3 with 28 day strength normally ranging from 0.2 to 10N/mm2 or more.
A widely cited definition of foamed concrete is: “A cementitious material having a minimum of 20 percent by volume of mechanically entrained foam in the plastic mortar or grout”
This differentiates it from air entrained concrete which has a far lower volume of entrained air (typically3–8%), retarded mortar systems (typically 15–22%) and aerated concrete where the bubbles are chemically formed.
In the production of foamed concrete, a surfactant is diluted with water and passed through a foam generator which produces a stable foam. This foam is then blended into a cementitious mortar or grout in a quantity that produces the required density in the foamed concrete.
Surfactants are also used in the manufacture of Low Density Fills (also called Controlled Low Strength Material (CLSM)). In this case, however, they are added directly into a sand rich, low cement content concrete to give 15 to 25% air. Somewhat confusingly, some suppliers of Low Density Fills refer to these materials as foamed concrete, but as the foam is not formed separately to the concrete they are not true foamed concretes.